
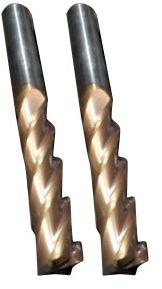
These end mills are generally used for roughing operation, whereas traditional end mills are still used for finishing and work where a smaller diameter is required.Įnd mills are sold in both imperial and metric shank and cutting diameters. For the time being however, this only generally applies to larger diameter end mills, at or above 3/4 of an inch. Another advantage of indexable end mills(another term for tools with inserts) is their ability to be flexible with what materials they can work on, rather than being specialized for a certain material type like more traditional end mills. It is becoming increasingly common for traditional solid end mills to be replaced by more cost-effective inserted cutting tools (which, though more expensive initially, reduce tool-change times and allow for the easy replacement of worn or broken cutting edges rather than the entire tool).

While more expensive, due to more complex design and manufacturing process, such end mills can last longer due to less wear and improve productivity in high speed machining (HSM) applications. Some modern designs also include small features like the corner chamfer and chipbreaker. There exist end mills with variable flute helix or pseudo-random helix angle, and discontinuous flute geometries, to help break material into smaller pieces while cutting (improving chip evacuation and reducing risk of jamming) and reduce tool engagement on big cuts. Bergstrom of Weldon Tool Company in 1918. Straight flute end mills were also used historically for metal cutting before invention of helical flute end mill by Carl A. Straight flute end mills (helix angle 0°) are used in special applications, like milling plastics or composites of epoxy and glass. For finishing end mills, it is common to see more tight spiral, with helix angles 45° or 60°. Each category may be further divided by specific application and special geometry.Ī very popular helix angle, especially for general cutting of metal materials, is 30°. Several broad categories of end- and face-milling tools exist, such as center-cutting versus non-center-cutting (whether the mill can take plunging cuts) and categorization by number of flutes by helix angle by material and by coating material. Not all mills can cut axially those designed to cut axially are known as end mills.Įnd mills are used in milling applications such as profile milling, tracer milling, face milling, and plunging. While a drill bit can only cut in the axial direction, most milling bits can cut in the radial direction. It is distinguished from the drill bit in its application, geometry, and manufacture. An end mill is a type of milling cutter, a cutting tool used in industrial milling applications.
